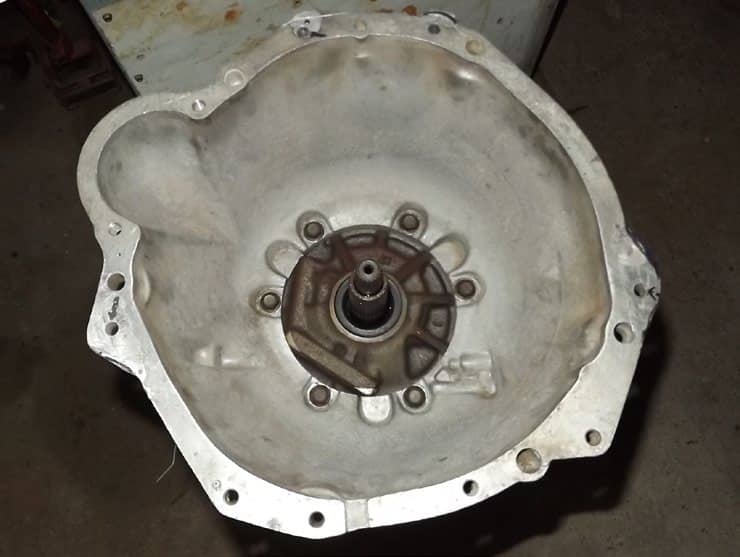
AUTOMATICALLY RODDING
This story is from the May 2021 edition of Australian Street Rodding.
Start your 7-day Magzter GOLD free trial to access thousands of curated premium stories, and 8,500+ magazines and newspapers.
Already a subscriber ? Sign In
This story is from the May 2021 edition of Australian Street Rodding.
Start your 7-day Magzter GOLD free trial to access thousands of curated premium stories, and 8,500+ magazines and newspapers.
Already a subscriber? Sign In
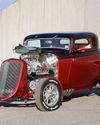
Built To Boogie
Joe Pega’s full size Hot Wheels coupe was...
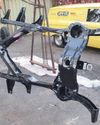
How-To Paint The Caddy Chassis
Preparing and painting a chassis at home
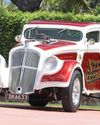
NITRO METHANE
Shaun and Tracey Pask’s wicked ’33 Willys gasser...
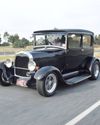
Searle's Street Rod Tudor
Alan’s A Model is home built hot rodding at its best...
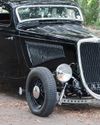
LIL' BLACK DELUXE
ANDREW SCRIM'S 1934 FORD FIVE WINDOW COUPE IS A HOT ROD WITH A RICH HISTORY...
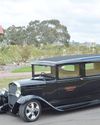
The Hot Rod Hearse
Oakdale Funerals team up with Detroit Chassis to deliver a classy Model A worthy of any hot rodders final ride...
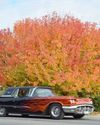
1960 FLAME BIRD
THIS MILD CUSTOM THUNDERBIRD MADE ITS WAY TO CENTRAL VICTORIA FROM CALIFORNIA...
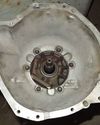
Technical Workshop
The column wherein all your questions relating to the technical aspects of hot rodding can be answered by our technical consultant, Ted Robinette. write to: p.o. box 232, Castlemaine 3450. email: info@graffitipub.com.au
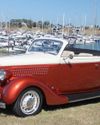
Hallett's '35 Convertible
Pieced together over a six year period using bits from a sedan and a coupe...
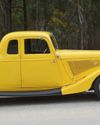
Sainty's Aussie Street Rod
Greg and Karen’s coupe has been on the road for 39 years...