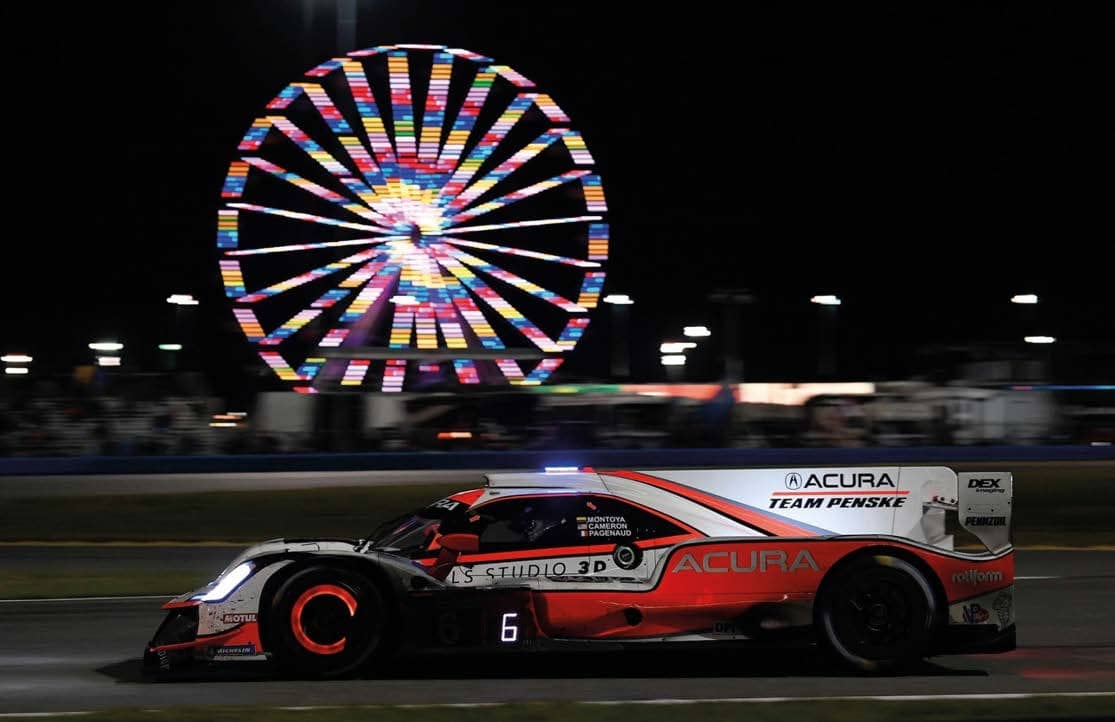
Thermal efficiency is a term that has been thrown around engineering circles for decades. While not necessarily immediately obvious in definition, it is one of the primary measures of internal combustion engine performance.
Last month, Racecar Engineering explored the journey of efficiency, specifically within Formula 1 development, over the last years. Building on that, in this article we will explore the technical advancements in depth with the aim of understanding how they have advanced the combustion process to extract maximum energy from fuel.
Being a hydrocarbon, petrol contains chemical energy that, upon oxidisation (combustion) is released as heat energy. The energy contained within the atomic bonds of a fuel is measured by the amount of heat released in its combustion, in joules (J), which establishes the link between the amount of fuel burned and the heat, or thermal input.
In the context of engine performance, measuring thermal efficiency allows us to satisfy questions such as how much fuel is needed to generate a particular amount of engine power?
Considering a more technical definition, we understand it as the engine output (kW) measured at the flywheel, divided by the fuel energy (kW) supplied to the engine. The two have an inversely proportional relationship so, if the fuel required for a given power output decreases, thermal efficiency increases.
Road car engines have been focussing intensely on maximising thermal efficiency for decades now, as lower fuel consumption is a clear selling point for any potential consumer. Motorsport, on the other hand, hasn’t traditionally shared the same concerns. Historically, power has been generated without much emphasis on efficiency, but nowadays the two sectors are steaming ahead on the same mission, just with very different driving forces.
This story is from the June 2020 edition of Racecar Engineering.
Start your 7-day Magzter GOLD free trial to access thousands of curated premium stories, and 8,500+ magazines and newspapers.
Already a subscriber ? Sign In
This story is from the June 2020 edition of Racecar Engineering.
Start your 7-day Magzter GOLD free trial to access thousands of curated premium stories, and 8,500+ magazines and newspapers.
Already a subscriber? Sign In
Talk the torque
More thoughts on in-wheel motors and their effects on twisting force
Rolling about
An explanation of the limitations of a previous load transfer article, bringing jacking forces into the mix
F1 breaks schedule records
The FIA has confirmed no fewer than 23 races on the 2022 Formula 1 World Championship schedule, the highest number of grands prix ever to be held in a single season, and that has led to criticism from some teams that will be on the road for eight months.
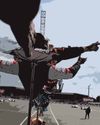
Under pressure
Toyota may have finished first and second at Le Mans this year, but the effort required to overcome a fuel delivery problem and finish with both cars was Herculean
Physics at work
Dutch company, Intrax, offers Racecar Engineering an insight into the technologies it employs to optimise its suspension products
Williams' 2030 ambition
Williams Racing has committed to becoming climate positive by 2030 as part of an all-new sustainability strategy.
Diff'rent strokes
Racecar looks at the different types of mechanical differential, their benefits and limitations
Das Boot
A curious Twitter exchange fired up a unique, hydrogen-powered, cross-country project that will contest the Baja 1000 in November 2022
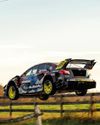
Air born
Every racecar engineer's dream is a blank sheet of paper design. When Hoonigan and Subaru approached Vermont Sportscars about building the next generation of Gymkhana racer, that's just what the company was given
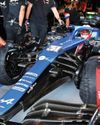
Remote control
Called variously ‘virtual garages’, ‘mission control’ or ‘race support rooms’ is the future of race engineering sitting in the warm back at HQ?