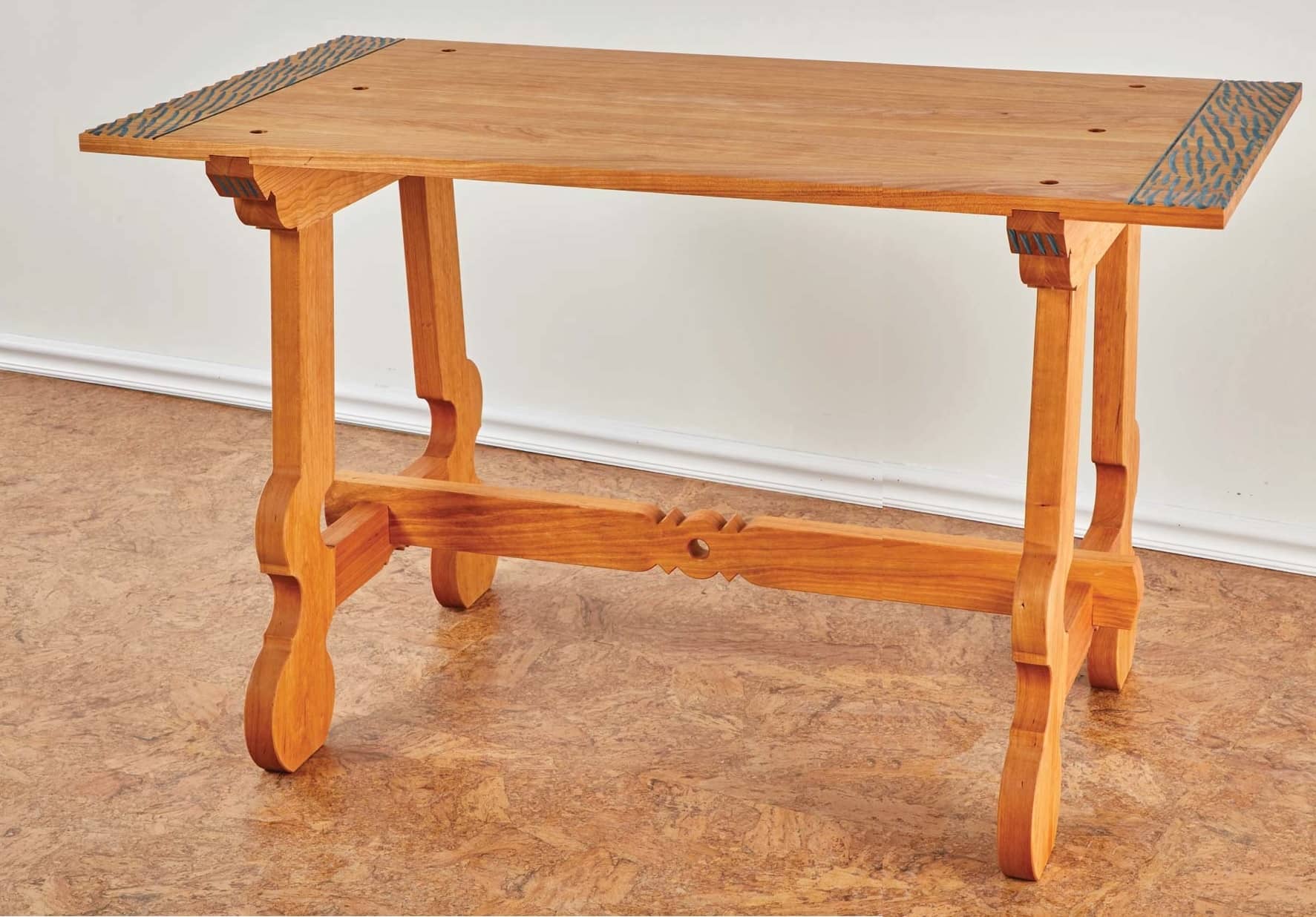
PROJECT #2107_
Skill Level
Intermediate
Time: 5 days
Cost: $350
One of the unique features of this table is its ability to be disassembled and tucked away. It's also very scalable. If the surface area (or lack thereof) is an issue, create a larger top and increase the length of the stretcher.
The inspiration for this project originated during a recent trip I took to visit my brother in Milwaukee, Wisconsin. The activity list for such occasion typically includes a stop at the Milwaukee Art Museum, catching a show at the Oriental Theatre, and some social imbibing down by the lakefront. It wasn’t until recently (after partaking in the latter of the activities listed above) that I discovered an old palatial estate on a bluff that overlooked Lake Michigan. To my surprise, it turned out to be a place called “Villa Terrace,” a decorative-arts museum that was once a private residence belonging to a couple named Lloyd and Agnes Smith at the beginning of the 20th century. Known as Sopra Mare (“above the sea” in Italian) to the Smiths, this resplendent piece of architecture is extraordinary beyond description.
This story is from the June 2021 edition of Popular Woodworking.
Start your 7-day Magzter GOLD free trial to access thousands of curated premium stories, and 8,500+ magazines and newspapers.
Already a subscriber ? Sign In
This story is from the June 2021 edition of Popular Woodworking.
Start your 7-day Magzter GOLD free trial to access thousands of curated premium stories, and 8,500+ magazines and newspapers.
Already a subscriber? Sign In
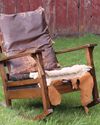
Woodworking Techniques Restoring an Antique Rocking Chair
Bring new life to a tired antique. Here are my steps to restoring an old rocking chair
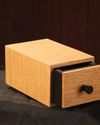
CRAFTING MAGIC: Making a Drawer Box
One of magic's oldest box tricks.
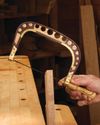
Laminated Coping Saw
This project brings together a diverse set of skills including epoxy work, bent lamination, metalworking, turning, and riveting
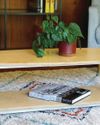
Mid-Century Media Console
This Mid-Century table is a great way to blend woodworking with modern materials
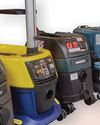
Tools 101 Calling all Dust Extractors
We take a look at eight dust extractors to see which ones stand out and which ones suck the most
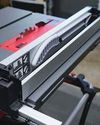
SawStop Compact Table Saw
Most woodworkers are familiar now with the SawStop line of table saws
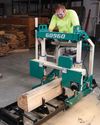
Grizzly Electric Sawmill
As a sawmill owner, I cut lumber for a variety of outlets. Most, I cut for myself
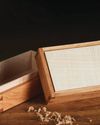
Veneered and Dovetailed Box
A box like this one is the perfect way to polish your hand tool skills and play with new techniques.
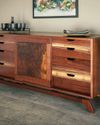
Mid-Mod Sideboard
All the flavors of walnut shine in this versatile storage and serving piece.
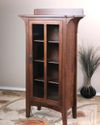
Limbert Style #357 Bookcase
Traditional construction techniques make this mediumsized bookcase a real gem.