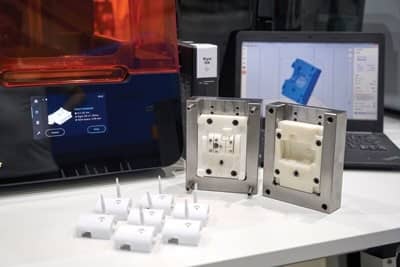
Injection molding is one of the leading processes for manufacturing plastics. It is widely used for mass-producing identical parts with tight tolerances. It is a cost-effective and extremely repeatable technology that yields high-quality parts for large series. It can produce volumes from 1,000 to 100,000+ of parts at very low unit costs.
Injection molding has a short cycle time, with each machine capable of building new parts every 15 to 60 seconds. It is a fast, intensive process where high heat and pressure are involved to melt thermoplastic and force it inside a mold. Because of these extreme molding conditions, the tools are traditionally made of metal by using a CNC machine or electric discharge machining (EDM). These are expensive industrial methods that require specialised equipment, high-end software, and skilled labour. As a result, the production of a metal mold typically takes four to eight weeks. For smaller part quantities, the cost, time, specialised equipment, and skilled labour required to fabricate the mold out of common tooling metals and manufacturing methods often makes injection molding at this scale unobtainable.
Esta historia es de la edición Aug-Sept 2021 de ET Polymers.
Comience su prueba gratuita de Magzter GOLD de 7 días para acceder a miles de historias premium seleccionadas y a más de 8500 revistas y periódicos.
Ya eres suscriptor ? Conectar
Esta historia es de la edición Aug-Sept 2021 de ET Polymers.
Comience su prueba gratuita de Magzter GOLD de 7 días para acceder a miles de historias premium seleccionadas y a más de 8500 revistas y periódicos.
Ya eres suscriptor? Conectar
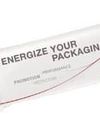
TotalEnergies and Jindal Films To introduce Certified Circular Polypropylene
TotalEnergies and Jindal Films have joined forces to produce more sustainable flexible food packaging and labels. Using advanced recycling technology from Plastic Energy, TotalEnergies will supply Jindal Films with Certified Circular Polypropylene produced from postconsumer plastic waste. This new value-chain collaboration will divert plastic waste currently destined for incineration and landfill because it is too complex to recycle through existing schemes.
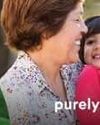
Lenzing's VEOCEL™ Brand Launches Hydrophobic Lyocell Fibres With Dry Technology
In its quest to drive greater sustainability in the personal care and hygiene industry, the VEOCEL™ brand has launched a new offering: VEOCEL™ branded lyocell fibres with dry technology which are naturally smooth and gentle on skin, ensuring comfort for sensitive skin. Absorbent hygiene products are an indispensable part of many consumers’ lives and are relied upon daily. As these are essential items, it is important that they should offer maximum comfort and relief to the user. This is demonstrated by the new VEOCEL™ branded lyocell fibres which have the capacity to provide a high level of comfort, softness and dryness, when applied in these types of products.
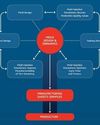
Simulating Injection Molding for Efficiency
Producing high-quality, plastic injection-moulded parts more quickly and cost-effectively has become a critical factor for manufacturing success in today’s global market. Instead of engaging in slow, expensive prototype iterations and test cycles to satisfy manufacturing requirements, designers, mold makers, and manufacturing professionals can leverage SOLIDWORKS® Plastics mold-filling simulation software to optimise parts for manufacturability, refine tooling to improve quality and shorten cycle times to reduce manufacturing costs

Perfecting your Purging Procedures
Determining the source of streaking or contamination in your molded parts is a critical step in perfecting your purging procedures, ultimately saving you time and money. We take a closer look at the nitty-gritty details of purging.
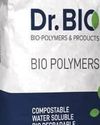
Going Sustainable With Polymers
Hi-Tech International is the first company in the country to manufacture a plantbased bio-polymer – Dr Bio – which can be used to replace single-use and multi-use plastic products with bio-compostable plastic. The Machinist take a closer look…
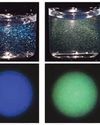
Inspired by Nature
A project researching the effects of structural colouration in nature and translating the same for pigmentation in industrial applications
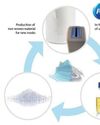
Face (mask) Off: Recycle & Reuse
Fraunhofer, SABIC, and Procter & Gamble join forces in a closed-loop recycling pilot project for single-use facemasks
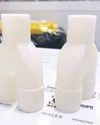
ELIX Polymers Joins The Fight Against Covid-19
Leading ABS producer ELIX Polymers is collaborating with a large group of companies within ClusterMAV, the Advanced Materials Cluster of Catalonia, Spain, in the fight against COVID-19.
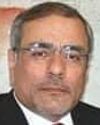
Investing in the Future
Umesh Anand, Managing Director, HPL Additives Limited talks to us about his company and its focus on innovation and sustainability
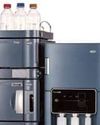
Waters Peptide Multi-Attribute Method for BioAccord System Boosts Innovator and Biosimilar Drug Development
Waters Corporation today introduced a new peptide multi-attribute method (MAM) workflow for the Waters™ BioAccord™ LC-MS System, enabling drug development, manufacturing, and QC scientists to monitor efficacy and safety through the analysis of critical quality attributes (CQAs) of monoclonal antibodies (mAbs) and other protein-based drugs.