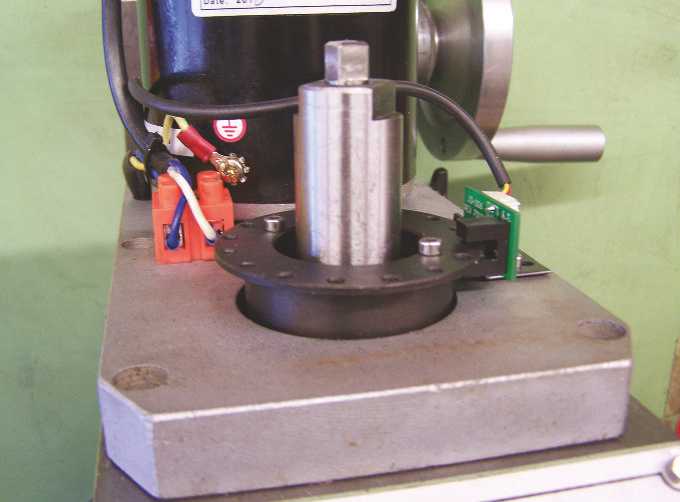
Introduction
I was starting to make a drill sharpening jig which required a slot to be milled at a precise angle, so I set up a pair of toolmaker’s buttons on the mill table to use a sine-bar to set the angle. When I came to use the dial indicator to set the buttons parallel to the table, I realised that holding the dial indicator in the spindle required that the spindle had to be prevented from rotating in order to be able to obtain a satisfactory reading. This required a lot of head scratching and thinking as to how I could build a spindle hold without altering the machine itself.
I hesitated to call this a spindle lock, as that would suggest that the spindle was well and truly locked and should allow quite a bit of torque to be used. This is not the case – it merely serves to hold the spindle from rotating whilst the DTI is used. Similarly, I did not call it a spindle brake, as this might imply a method of bringing the spindle to a stop whilst it is rotating, so I decided to call it a spindle hold.
My first and primary objective was to make it such that no alterations were made to the milling machine at all. I found that I could not achieve this objective fully, as I did end up having to drill an access hole for the screw to operate the spindle hold. I considered that a single 7mm diameter hole in the plastic cover over the motor and spindle was acceptable. Otherwise, there are no irreversible alterations to the milling machine.
This story is from the December 2019 edition of Model Engineers' Workshop.
Start your 7-day Magzter GOLD free trial to access thousands of curated premium stories, and 8,500+ magazines and newspapers.
Already a subscriber ? Sign In
This story is from the December 2019 edition of Model Engineers' Workshop.
Start your 7-day Magzter GOLD free trial to access thousands of curated premium stories, and 8,500+ magazines and newspapers.
Already a subscriber? Sign In

Desktop Gear Hobbing
Toby Kinsey has designed this fascinating piece of gearmaking equipment

The John Stevenson Trophy 2020
Many readers and forum members will remember John Stevenson, a contributor to MEW but best known for his larger-than life presence on the Model Engineer forum.

From the Archives: Twist drill Sharpening by the Four Facet Method
Giles Parkes, MEW Issue 64, February/March 2000

A Storage Story
Robin King shares the lessons learned from his experience of workshop moves

A Simple Drill Grinding Aid
A newcomer to our hobby was having trouble sharpening drills, so Howard Lewis made a simple aid for him

Yet Another Bodge-Up!
Peter Shaw finds a use for some aged homebrew slot drills.

Garden Tractor Refurbishment
Stan Nesbitt uses his workshop to rescue some garden machinery.

Theasby's Wrinkles A Lashed Up Lathe
Geoff Theasby makes a temporary lathe for a long, thin rod in the middle of the night

Opening the spindle bore on a Mill
Brian Wood had to enlarge the bore on his Dore-Westbury Mk II miller

A Rotary Table from Scrap
Terry Cleife explains an interesting approach to improvising a rotary table