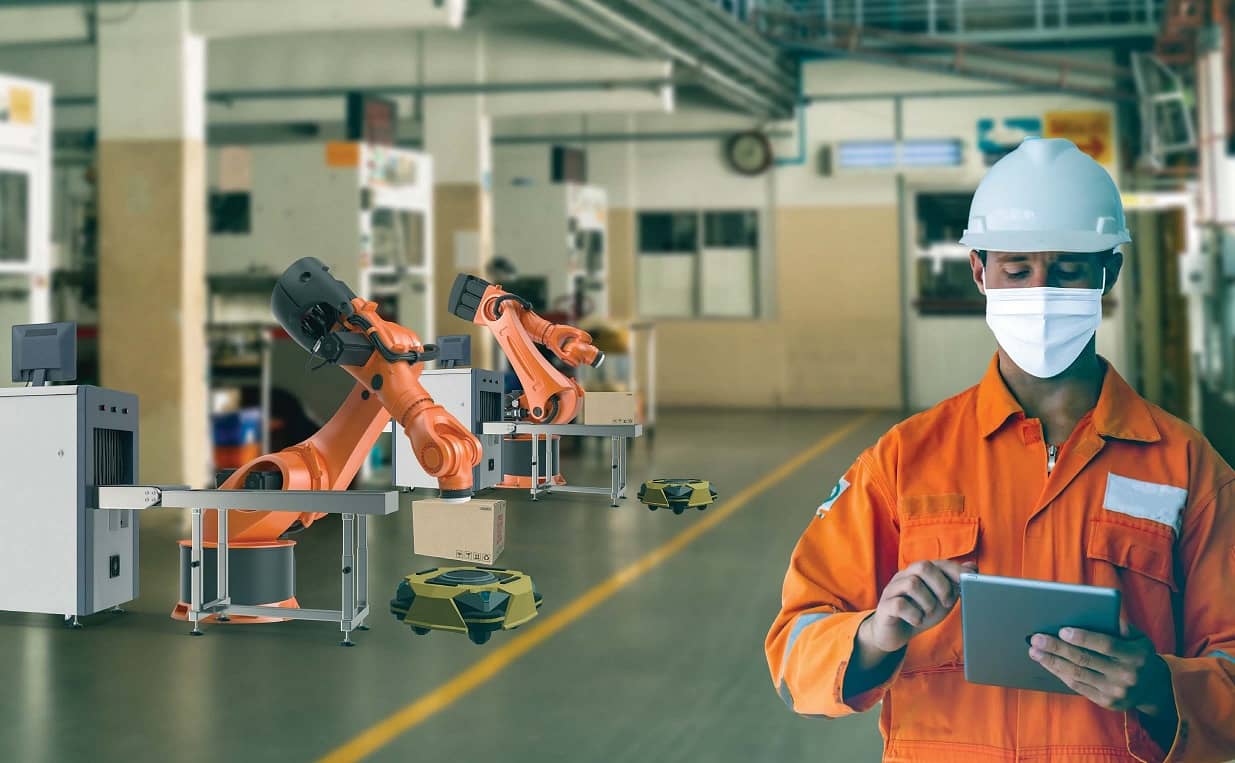
WITH MUCH OF THE WORLD CONTINUING TO stay under lockdown in varying degrees, normal activities continue to be affected. The virus shows no signs of abating and just when one lets one’s guard down, there seems to be a surge of fresh cases. But life must go on. In a sense, work-from-home fatigue has set in most people and there is a kind of longing for the ‘good old days’. But that is not to be. Not for a long time to come.
Manufacturing Today explores what the New Normal means to various companies, their way of rejigging schedules, and some of the steps taken to combat longterm effects of covid-19.
Safety concerns are top priority. One can never be too safe. Accidents are waiting to happen. However, taking precautionary measures is primal human nature. And more so today.
Ramakant Reddy, MD, LMT Tools India, says, “The covid-19 situation is unprecedented. Manufacturing PMI fell to 27% in April from around 52% in March. I think this was the lowest reading in the last 15 years. During the initial phase of the lockdown, we invested our time in planning the New Normal. Our HR prepared comprehensive guidelines for resuming operation post lockdown which are updated from time to time. The IT team worked on solutions to keep us connected to customers as well as our employees across the world, while the sales & marketing team connected with customers by sending regular updates and conducted online training for customers on new technologies in gear manufacturing, special programmes in Die and Mould, and addressed issues faced in milling & tapping.”
This story is from the October 2020 edition of Manufacturing Today.
Start your 7-day Magzter GOLD free trial to access thousands of curated premium stories, and 8,500+ magazines and newspapers.
Already a subscriber ? Sign In
This story is from the October 2020 edition of Manufacturing Today.
Start your 7-day Magzter GOLD free trial to access thousands of curated premium stories, and 8,500+ magazines and newspapers.
Already a subscriber? Sign In
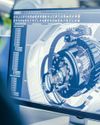
Precision Revolution
Exploring the fusion of Machine Learning and CAD/CAM Technologies, Shriyal Sethumadhavan delves into the transformative impact of AI integration in manufacturing.
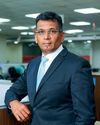
Empowering MSMEs
In conversation with Amit Mande, Chief Revenue Officer, U GRO Capital
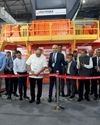
Fornnax unveils SR-200 HD recycling innovation
Fornnax Technology continues to expand its portfolio of high capacity lines and debuted an upgraded variant of primary shredder.
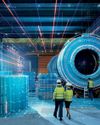
Transforming manufacturing and product development
India's manufacturing sector, currently contributing 17% to the GDP, is expected to be one of the key drivers of growth for the country.
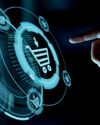
Transforming E-commerce: How LLMs are changing visual content
LLMs reshape e-commerce with captivating visuals, balancing benefits and drawbacks of authentic content in the digital retail arena
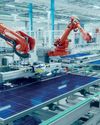
An intelligent move
Dive deep into the future of manufacturing as we explore the transformative power of intelligent technologies revolutionising the industry.
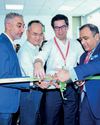
Meeting India's data centre cooling demands
Schneider Electric inaugurates state-of-the-art cooling factory in Bengaluru
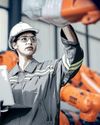
The gender matters of manufacturing
Does the manufacturing industry suffer from a gender gap?
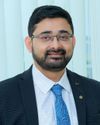
Navigating India's manufacturing landscape
Jibak Dasgupta, Director General and CEO, Indian Machine Tool Manufacturers' Association's view on the influx of investments and the manufacturing landscape
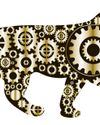
A decade of 'Make in India': The foundation for building a manufacturing powerhouse
As India experiences profound economic growth, it has emerged as the second most sought-after manufacturing destination in the world, contributing 13.9%1 to the economy.